Frequently asked Questions
Concrete engineering advice
Business contact
Trends and New Technologies in the Concrete Construction Industry
Amid the continuous development of the construction industry, concrete - a key building material - is also undergoing significant changes in technology and trends. From improving mechanical properties to reducing environmental impact, new technologies and modern trends are opening up numerous opportunities and challenges for the concrete industry. In this article, we will explore noteworthy innovations and prominent trends shaping the future of concrete construction.
1. Advanced Construction and Finishing Materials
To date, the European Commission estimates that product innovation in the entire construction industry accounts for up to 70%. As such, materials are a powerful lever for innovation.
Table: Recent Advances in Construction and Finishing Materials
Improvement of Traditional Materials and Their Features | Combination of New Materials and Diverse Features | New Materials with Completely New Features |
---|---|---|
iQ Natural - an advanced vinyl flooring that is 100% recyclable and uses bioplasticizers. This product meets the TVOC (volatile organic compounds) criteria at a level 100 times below the strictest European standards. | Ultra-light ceramic tiles - using quick-setting cement with added organic fibers to halve the weight. | Rainwater-absorbing roofs, which can significantly reduce the energy needed for air conditioning. |
Neopor - an advanced styropor foam insulation board, with 20% superior insulation efficiency. | Addition of bacterial spores in concrete to achieve self-healing concrete, reducing maintenance costs by 50% over the entire life cycle of the building. | Micronal - a phase change material used to make building materials, efficiently managing temperature in an intelligent manner. |
Organic-coated steel (by ArcelorMittal) achieves a durability of 30 years and contains no harmful agents. | Concrete using chemical additives that can reduce curing time by 50% (*). | Hollow tile surfaces with smooth, non-porous surfaces creating super water-resistant surfaces. |
- Concrete curing (or thermal-moisture curing) is the process of providing high-temperature steam under normal pressure (room pressure) to enhance the setting process of concrete, preventing surface cracks and ensuring even setting inside.
In the current market, advanced construction materials have been penetrating the Vietnamese market. However, these new materials still face challenges in market penetration, let alone achieving wide acceptance, despite their significant potential. This is particularly true for developing countries.
The main reasons include:
- Advanced finishing materials require a substantial initial investment, while the benefits are often recognized over the entire lifecycle of the building.
- New advanced materials have not yet proven their superiority in practical applications.
- Investors and decision-makers in construction companies may not be updated on the latest developments or lack the necessary information to make purchasing decisions (issues such as price, durability quality, and ecological value).
2. Standardization, Modulation, and Prefabrication
Enhancing productivity in the construction sector can be achieved through standardization, modulation, and the use of prefabrication. Standardizing construction components brings numerous benefits such as cost reduction, improved quality, and increased product reliability, while also reducing future maintenance costs and expanding recycling potential.
Modulation further enhances the advantages of standardization by creating greater flexibility and customization, while exploring the potential of prefabrication in a manufacturing environment. Prefabrication can improve construction performance by optimizing workflow sequences and reducing weather-related downtime. As a result, prefabrication can shorten project completion times and reduce costs compared to traditional methods, while also providing safer working conditions for workers.
Prefabrication Challenges:
- Poor image, lack of experience in applying prefabrication;
- Individualized customer demands;
- Lack of commitment from suppliers, especially when the market is immature and alternative options are not immediately available;
- The customized and irregular nature of construction demand leads to workshops not fully utilizing space;
- High transportation costs, especially when the distance between the factory and the construction site is large or when transport links are inadequate;
- Difficulty assembling large prefabricated components due to space constraints at the construction site;
- Technical regulations from project owners (e.g., in Spain, public investment projects prohibit the use of prefabricated bridge foundations).
Strategies to Mitigate Prefabrication Risks:
- Develop industry standards for component sizes or robust joints to reduce commitment risks.
- Continue developing modular construction systems and closely collaborate with suppliers to enhance applicability and create systems suited for affordable housing needs in urban areas.
- Perform economic and supply feasibility assessments of these technologies during planning and adjust construction processes at the site to use prefabricated or modular components; this helps determine the full productivity potential of prefabrication.
- Closely collaborate with customers and advocate for the benefits of prefabrication, including considering repurposing or adjustments after construction to meet future demands.
- Adopt and promote new construction concepts to bring innovation and progress in the construction industry.
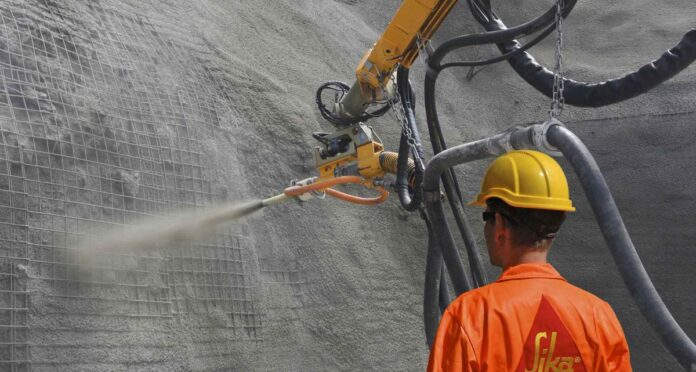
3. Automated (Semi-Automated) Construction Equipment
Automated construction equipment, also known as semi-automated, plays a crucial role in increasing productivity in the construction industry. Machines such as excavators, bulldozers, drills, pile drivers, conveyors, pumps, and cranes have become indispensable tools, helping move, excavate, pour concrete, and install components efficiently and quickly.
While many industries have advanced significantly in adopting Industry 4.0 technologies, the construction sector has yet to fully automate. However, with the progress of robotics technology, this situation may change significantly.
New Technologies Driving Innovation in Construction Equipment:
- Drones, low-cost sensors, remote and automated control systems could be major drivers of innovation in construction equipment.
- Automated and semi-automated equipment holds great potential with numerous benefits. They help reduce construction costs by shortening completion times and project handovers, while also increasing labor productivity.
- High precision and fewer errors of these devices help improve construction quality. Additionally, they play an important role in enhancing safety by keeping workers away from hazardous areas.
Steps for Companies in the Value Chain to Enhance Automation:
- Embrace technology trends: Seamlessly integrate physical and digital systems to create a foundation for comprehensive automation.
- Innovate: Implement smart project designs, promoting the use of prefabricated and modular systems to optimize processes.
- Thorough preparation: Plan in detail and prepare technical foundations for the construction site, ensuring effective deployment of automation.
- Enhance connectivity: Establish unified industry standards, especially regarding communication protocols, to ensure interoperability and widespread application of automated devices.
- Optimize resources: Apply early exploitation models to efficiently utilize existing equipment, enhancing investment efficiency.
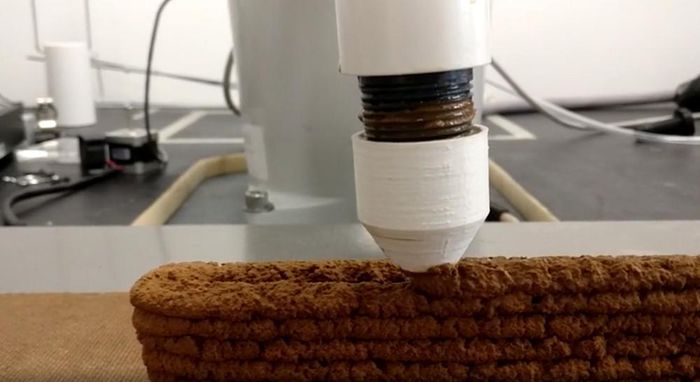
4. New Construction Technology - 3D Printing
The 3D concrete printing method is a promising new trend in civil construction. This solution allows for accelerated construction speed and reduced apartment construction costs.
3D FDM printers are used to print concrete instead of using thermoplastic materials as before. 3D printed concrete contains a special additive similar to superplasticizers, preventing clumping and enhancing the flow efficiency of the concrete.
Potential 3D Printing Methods:
- Contour Crafting is one of the potential 3D printing methods, capable of working effectively in various environments.
- 3D concrete printing opens up vast opportunities for concrete manufacturers. With 3D concrete printing technology, manufacturers can create concrete products with higher precision and fewer errors.
- This improves product quality and increases market competitiveness. However, this will be a solution for the future, as current techniques are not yet fully developed for complete implementation.
The above information provides insight into the trends and new technologies in the concrete construction industry. What do you think about the development of these technologies? Share your thoughts in the comments below.
If you are looking for a reliable supplier of ready-mix concrete in large quantities, SMC is ready to be your trusted partner.
Following the new trends in the concrete construction industry, we can see the application of new materials and 3D construction technology.
Specifically, advanced construction and finishing materials offer numerous benefits and superior protection during future use. Additionally, we should pay attention to standardization, modulation, and prefabrication.
While there are many advantages to the new concrete construction trends, there are also many challenges. To understand this better, please refer to the article: “Trends and New Technologies in the Concrete Construction Industry” shared by SMC.
Other news
Currently, ready-mix concrete is a top choice for many construction projects—both large and small—thanks to its convenience, consistent quality, and high construction efficiency. With extensive experience supplying commercial concrete for numerous key projects in the Southern region, SMC proudly offers a diverse range of ready-mix concrete products to meet the technical requirements of every type of construction.
A Comprehensive Guide to Concrete Specs – Everything You Need to Know
A Complete Guide to Concrete Specs – a set of technical parameters including concrete grade, slump, compressive strength, aggregate size, and mix ratio. This article helps you understand how to define, apply, and control concrete quality according to TCVN standards and practical construction conditions.
How to check the concrete slump
In construction and civil engineering, concrete slump test (or simple slump test) is the work performed at the construction site or in the laboratory that usually determines and measures the hardness, consistency of samples. Concrete before pouring concrete or casting maintenance, research or experiment samples.